The Scientific Research Behind Porosity: A Comprehensive Overview for Welders and Fabricators
Recognizing the intricate systems behind porosity in welding is important for welders and producers pursuing remarkable workmanship. As metalworkers delve right into the depths of this sensation, they discover a world governed by numerous variables that affect the development of these tiny spaces within welds. From the composition of the base products to the ins and outs of the welding procedure itself, a plethora of variables conspire to either intensify or alleviate the visibility of porosity. In this detailed overview, we will certainly untangle the scientific research behind porosity, discovering its impacts on weld top quality and introduction progressed techniques for its control. Join us on this journey through the microcosm of welding imperfections, where accuracy satisfies understanding in the quest of perfect welds.
Recognizing Porosity in Welding
FIRST SENTENCE:
Examination of porosity in welding exposes crucial insights into the honesty and top quality of the weld joint. Porosity, identified by the presence of cavities or voids within the weld steel, is an usual worry in welding procedures. These spaces, otherwise properly resolved, can endanger the structural honesty and mechanical properties of the weld, bring about possible failings in the completed product.

To find and quantify porosity, non-destructive screening techniques such as ultrasonic testing or X-ray examination are typically used. These strategies enable the recognition of inner problems without compromising the integrity of the weld. By examining the size, shape, and distribution of porosity within a weld, welders can make educated choices to improve their welding procedures and attain sounder weld joints.
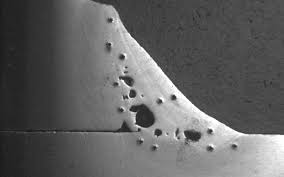
Variables Influencing Porosity Development
The occurrence of porosity in welding is influenced by a myriad of aspects, varying from gas securing efficiency to the complexities of welding criterion settings. One vital aspect adding to porosity formation is poor gas securing. When the shielding gas, normally argon or CO2, is not properly covering the weld swimming pool, climatic gases like oxygen and nitrogen can infect the molten metal, leading to porosity. In addition, the tidiness of the base products plays a substantial role. Impurities such as corrosion, oil, or moisture can vaporize throughout welding, creating gas pockets within the weld. Welding parameters, consisting of voltage, present, take a trip rate, and electrode type, additionally influence porosity development. Using inappropriate settings can create extreme spatter or heat input, which subsequently can result in porosity. The welding method utilized, such as gas steel arc welding (GMAW) or protected metal arc welding (SMAW), can affect porosity formation due to variations in warmth circulation and gas insurance coverage. Comprehending and controlling these aspects are vital for minimizing porosity in welding operations.
Results of Porosity on Weld Top Quality
The visibility of porosity likewise compromises the weld's resistance to deterioration, as the caught air or gases within the voids can respond with the surrounding setting, leading to destruction over time. Additionally, porosity can hinder the weld's capacity to endure pressure or influence, more endangering the overall high quality and dependability of the bonded structure. In critical applications such as aerospace, automotive, or architectural buildings, where security and longevity are paramount, the destructive results navigate to this site of porosity on weld high quality can have severe effects, emphasizing the relevance of lessening porosity via correct welding methods and treatments.
Techniques to Minimize Porosity
In addition, utilizing the suitable welding criteria, such as the correct voltage, current, and travel rate, is essential in preventing porosity. Keeping a regular arc length and angle during welding likewise helps reduce the possibility of porosity.

Using the appropriate welding technique, such as back-stepping or using a weaving activity, can likewise help disperse warmth evenly and lower the possibilities of porosity development. By carrying out these methods, welders can properly lessen porosity and produce top notch bonded joints.

Advanced Solutions for Porosity Control
Implementing cutting-edge modern technologies and innovative methods plays a pivotal duty in attaining superior control over porosity in welding processes. One advanced option is using sophisticated gas combinations. Securing gases like helium or a mix of argon and hydrogen can help in reducing porosity by giving much better arc security and enhanced gas insurance coverage. Furthermore, employing sophisticated welding methods such as pulsed MIG welding or modified atmosphere welding can additionally help alleviate porosity issues.
One more sophisticated solution includes making use of sophisticated welding devices. For example, using devices with integrated attributes like waveform control and sophisticated source of power can enhance weld quality and lower porosity threats. The execution of automated welding systems with exact control over specifications can substantially decrease porosity issues.
Moreover, including sophisticated tracking and inspection modern technologies such as real-time X-ray imaging or automated ultrasonic screening can help in discovering porosity early in the welding procedure, enabling instant corrective actions. Generally, incorporating these advanced more info here remedies can significantly improve porosity control and boost the total high quality of welded components.
Verdict
In conclusion, comprehending the scientific research behind porosity in welding is crucial for welders read the full info here and makers to produce top notch welds - What is Porosity. Advanced remedies for porosity control can even more enhance the welding process and ensure a strong and trustworthy weld.
Comments on “What is Porosity in Welding: Trick Factors and Their Impact on Weld Top Quality”